Learn about how corrugated became the obvious choice in protective packaging and what you need to know to select the perfect box.
When it comes to protecting products during shipment, the corrugated box is the most common choice for companies around the world. As a company dependent upon safe shipment of products and supplies, it’s important to understand the history of corrugated and product specifications so you can make an informed decision on what’s appropriate for your packaging and shipping needs.
History of Corrugated
Corrugated was originally made in England as a liner for tall hats in the 1850’s. It was not patented to be used as a shipping material until the 1870’s and was not developed into corrugated box form until the 1890’s. These early corrugated boxes were initially used for packaging glass and pottery containers. Wells Fargo was the first to test these boxes for light express deliveries in New York City. The demand for corrugated board ballooned after World War II, especially after the kraft process was developed in the South that made the pulp stronger and less expensive. By the 1970s, almost every product in the US was shipped in a corrugated fiberboard shipping container
For a more in depth history on box making, read: “The History of Corrugated Fiberboard Shipping Containers.”
Corrugated Product Specifications
Corrugated fiberboard can be specified by the construction (single face, single wall, double wall, etc.), flute size, burst strength, edge crush strength, flat crush, basis weights of components (pounds per thousand square feet, pounds per square inch, etc.), paper weights, and surface treatments and coatings. The combination of these elements determine the box’s overall strength and crush resistance.
Box Construction:
Corrugated can be constructed multiple ways, based on its intended use.
- Single Wall: Standard corrugated comprised of single fluting with two liners.
- Double Wall: Suitable for packaging heavier goods – this adds an additional layer of fluting and liners to single-wall construction.
- Triple Wall: To package extremely large and heavy items (like large machine parts), triple wall boxes add yet another fluting and liner.
Fluting:
The flute sizes refer to the number of flutes per linear foot. The most common flute size in corrugated boxes is “C” flute. The following chart from Wikipedia is a useful guide to the standard US corrugated flutes[4]:
Flute Designation | Flutes per Linear Foot | Flute Thickness (in) | Flutes per Linear Meter | Flute thickness (mm) |
---|---|---|---|---|
A flute | 33 +/− 3 | 3/16 | 108 +/− 10 | 4.8 |
B flute | 47 +/− 3 | 1/8 | 154 +/− 10 | 3.2 |
C flute | 39 +/− 3 | 5/32 | 128 +/− 10 | 4.0 |
E flute | 90 +/− 4 | 1/16 | 295 +/− 13 | 1.6 |
F flute | 128 +/− 4 | 1/32 | 420 +/− 13 | 0.8 |
In addition to the above flute types, D flute is an innovative new type of corrugated fluting available from Pratt Industries that is a great option for many types of packaging. It provides for superior printing and offers cost advantages for today’s warehousing and material handling challenges.
Box Design:
The most common box style is a Regular Slotted Container (RSC). In this design style, all of the closure flaps are the same length from the fold to the edge. Many other styles of corrugated boxes and structures are available:
- FOL (Full Overlap): A Full Overlap Box is similar to an RSC except the major flaps fully overlap. Full-overlap flaps provide extra stacking strength and edge protection.
- HSC (Half Slotted Container): Half-Slotted Containers (HSC) are similar to an RSC, but with only one set of flaps. They are useful when an open top container is desired. HSCs can be used to create a telescope box.
- A Full Telescope Box has two fully telescoping sections. The sections may be formed by staples, die-cut locks, adhesive, etc.
- A Partial Telescope Box has two sections. The top telescopes partially over the bottom.
- A corrugated tray is often used for display purposes or used with a shrink wrap.
- Corrugated corner pads can be used for product support and package cushioning.
- Special die-cut shapes have almost endless designs and uses.
Box Strength:
The strength of corrugated board can be assessed using the Bursting (Mullen) Test which measures bursting strength or the Edge Crush Test (ECT) which measures stacking strength. Bursting Test is a measure of the force required to rupture or puncture the face of corrugated board. This method has long been used in the industry. The newer standard, ECT, is a true performance test and takes a defined sample board size and measures the straight compression force for that size. PrattPlus.com carries a variety of corrugated board strengths, including 40 ECT, 44 ECT, and 48 ECT boxes.
Paper Weights:
The kraft paper used to make corrugated can be sourced as virgin pulp or OCC, old corrugated containers that are recycled into new paper. Common base paper weights are measured in pounds per square inch as follows:
- 23lb
- 26lb (popular industry standard)
- 29lb
- 31lb
- 33lb
- 35lb
- 42lb (popular industry standard)
Surface Coatings:
As an added protective measure, the liners of corrugated boxes and boards can also have special coatings, finishes or properties.
- Polythene / Polyethylene
- Anti Static & Conductive
- Colour Wash
- Water Resistant / Wax
- Fire Resistant
- Anti Abrasive
- Acid Free
- Post Consumer/Recycled
- Exposed Flute
- Foam Lined
About Pratt Industries Corrugated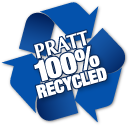
It takes the best raw materials to consistently produce good boxes, so we continually invest capital to ensure our fleet of corrugators is among the best in the industry. We solve packaging issues for customers on a daily basis, from package design and the role of the package in the manufacturing process to meeting distribution requirements and responding to consumer preferences. We are the world’s most diverse producer of linerboard products that offer best-in-class print-ability, strength, coatings and specialized performance characteristics.
Pratt Industries’ packaging is proudly made from post-consumer recycled fiber and all lines are completely recyclable. Pratt Industries also strives to continually reduce paper weights to eliminate costly over-packaging as well as reduce the environmental impact. Plus, in addition to our corrugated stock offerings on PrattPlus.com, Pratt Industries has the know-how and capabilities to deliver custom corrugated solutions. Customers know they can count on the company for superior products, services and innovation.